The Duty of Metal Stamping in Modern Production and Item Advancement
Exploring the World of Metal Stamping: From Style to Manufacturing
Within the world of production, steel marking attracts attention as a precise and effective technique for shaping metal sheets right into different types with exceptional uniformity. From the first layout stage where detailed patterns form to the detailed manufacturing procedures, steel stamping is a mix of artistry and design. Exploring this globe introduces an intricate interaction of imagination and technological mastery, providing a peek into a realm where innovation meets workmanship.
Background of Steel Stamping
Steel stamping, a widely used production procedure today, has a rich history that dates back to old times (Metal Stamping). The beginnings of metal stamping can be mapped to old worlds such as the Egyptians, who used marking methods to decorate jewelry and accessories with detailed styles. In time, metal marking progressed, with worlds like the Greeks and Romans utilizing it for developing coins and ornamental products

In the 20th century, metal marking remained to progress with the integration of automation and computer system numerical control (CNC) modern technology. These advancements better enhanced the performance and precision of steel stamping procedures, making it a vital component of modern manufacturing throughout industries such as auto, aerospace, and electronics. Today, steel marking stays an essential manufacturing procedure, incorporating custom with technology to meet the needs of a constantly evolving sector.
Design Factors To Consider and Prototyping
Design factors to consider in steel marking consist of product option, component geometry, tooling style, and manufacturing expediency. Tooling style plays a considerable function in the success of metal stamping projects, affecting part accuracy, tool longevity, and production performance.
Prototyping is a crucial phase in the steel marking procedure that enables engineers to test the design, confirm manufacturability, Discover More and make essential changes prior to full-blown production. Prototyping aids recognize prospective problems at an early stage, saving time and prices over time. It likewise provides a possibility to maximize the style for efficiency and top quality. By very carefully thinking about design facets and using prototyping, producers can streamline the steel stamping procedure and accomplish top quality, cost-effective manufacturing results.
Tooling and Tools Essentials
Taking into consideration the crucial function that tooling design plays in the success of metal marking projects, comprehending the essential tools and devices called for is critical for attaining efficient production end results. Tooling is a fundamental element of steel marking, as it directly influences the quality and consistency of the last items. Important devices consist of passes away, strikes, and components, which are custom-made to form and develop the steel right into the wanted parts. Dies are the primary device utilized to reduce and develop the steel, while strikes help produce openings or details shapes. Components hold the steel in position throughout the marking process, guaranteeing accuracy and repeatability. Furthermore, tools such as marking presses, my sources feeders, and coil handling systems are crucial for automating the stamping process and increasing productivity. Investing in top notch tooling and tools not just boosts manufacturing performance yet additionally brings about greater accuracy, lowered waste, and total price financial savings in steel stamping operations.
Manufacturing Process and Quality Assurance
Effectively taking care of the production procedure and implementing robust top quality control measures are necessary for ensuring the success of metal marking projects. The production procedure in steel stamping involves a collection of actions that need to be meticulously collaborated to attain optimal outcomes.
Quality control in metal stamping is critical to provide items that satisfy the needed requirements. Evaluating the stamped components at various phases of production helps identify any defects at an early stage, avoiding expensive rework or scrap. Methods such as dimensional assessment, visual evaluation, and material testing are commonly employed to ensure the quality of the stamped components. By keeping stringent quality assurance requirements, producers can support their credibility for delivering high-quality steel marked products.
Applications and Industry Insights
In the realm of metal marking, the effective application of manufacturing procedures and top quality control measures directly influences the efficiency and reliability of different market applications and supplies useful understandings right into the market's functional characteristics. Furthermore, steel stamping helps with the manufacturing of numerous home home appliances, consisting of refrigerators, cleaning machines, and stoves, by giving cost-efficient remedies for manufacturing durable and complex components. Understanding the applications and sector understandings of steel stamping is important for maximizing manufacturing procedures and boosting item top quality across various fields.
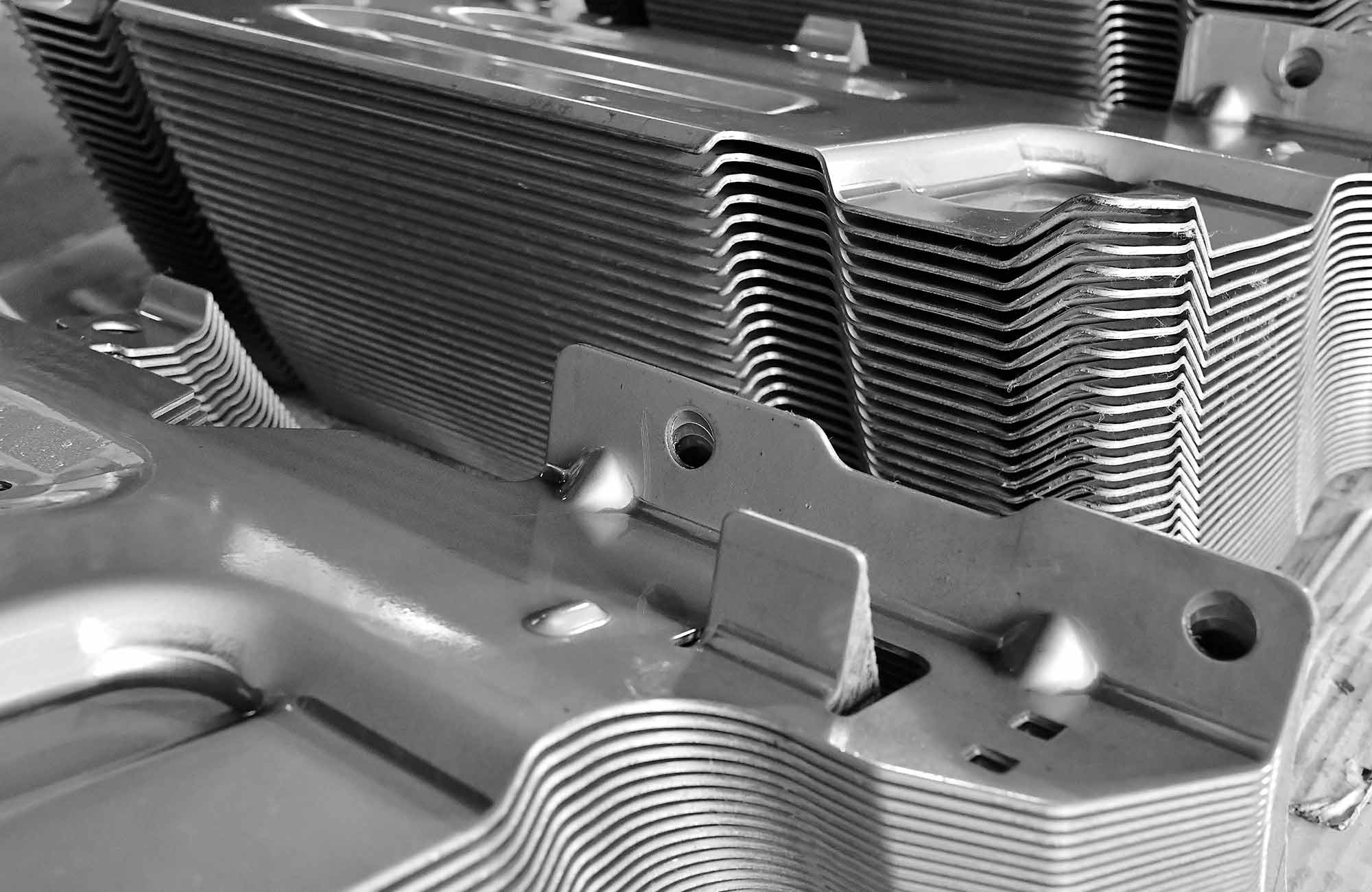
Final Thought
Design factors to consider, prototyping, tooling, equipment, manufacturing processes, link and high quality control are essential facets of steel stamping. With its prevalent applications and industry understandings, metal stamping proceeds to be a versatile and reliable manufacturing process.